Jon Lawson reports on the latest from a historically significant location for mining: the UK
Mining has had a long history in Britain, and greatly influenced its economic development. One of the earliest known mines is at Grime’s Graves in Norfolk, Eastern England, where Neolithic people excavated high quality flint over 5,000 years ago. They dug some 400 pits using tools made from deer antler.

A disused tin mine on the coastline of St Agnes, mid-Cornwall. There are over 200 of these iconic buildings in the South West of England. Credit: FreeImages.com/Andrew Dubock
In more modern times, the abundance of coal underpinned the industrial revolution, and at one time before WW1, one million men were employed underground and there were 200 pits in Wales alone. However the industry has declined, with many unprofitable pits closing during the Thatcher administration in the 1980s.
The last deep pit, Kellingley colliery in North Yorkshire, closed at the end of 2015. With the closure was the loss of over 400 jobs. The remaining mines produce around 12 million tonnes per year.
To gain an understanding of the current state of mining in Britain, in February 2016 the CBI published a report entitled The UK Mineral Extraction Industry. Even at a glance, the numbers further underline the importance of Britain’s natural resources: 210 million tonnes of mineral extraction per year, turning over £15 billion, providing 34,000 direct jobs and 4.3 million across the whole supply chain. Altogether this makes up 16% of the total UK economic turnover.
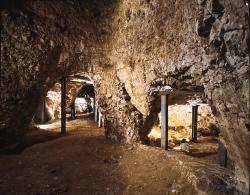
Visitors can experience life underground as a Neolithic flint miner at Grimes Graves in Norfolk.
The lion’s share is non-metallic, with around £6,133 million worth of building stone, limestone, gypsum, chalk and slate being produced, and £7,049 million worth of sand, gravel and china clays.
Many other materials are mined, including salt (6.6 million tonnes), peat (1 million tonnes) and potash (0.9 million tonnes).
That last figure looks set to be dramatically expanded with the news that the Sirius York Potash Project is now entering a crucial stage, and the Definitive Feasibility Study (DFS) is to be published as International Mining Engineer (IME) goes to press. The company says in a statement, “The completion of a DFS for such a large scale project is a very detailed process and there is a large amount of complex information from various suppliers, consultants and engineering firms that needs to be compiled, reviewed and then integrated into the final DFS. While this process is time consuming, it is vitally important for a project with an expected life of over 100 years that it is robust.”
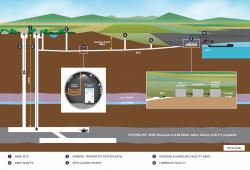
Schematic showing the mine to port plan.
Sirius is currently pondering the selection of the tenderers for the site preparation, mine shafts and mineral transportation system. Chris Fraser, managing director and CEO of Sirius told IME, “Sirius Minerals’ polyhalite project in North Yorkshire has a simple and efficient design from mine to port, enabling large-scale production in a way that is sensitive to the environment. As we continue to develop the project to become one of the world’s most significant producers of multi-nutrient fertiliser, we can deliver strong returns whilst creating jobs and prosperity in an area that can benefit greatly from this mine.
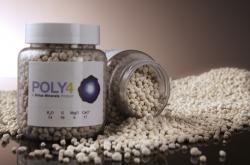
The end product – the UK currently produces around 0.9 million tonnes of potash per annum.
“Sirius secured the key planning approvals in 2015, which has enabled us to focus on the Definitive Feasibility Study for this world class project. The DFS will provide us with the economic parameters to execute a financing strategy that will bring the project into production. We look forward to beginning construction and developing a mine that delivers significant value to shareholders and meaningful revenue to both the local and national economy.”
On your metal
The glory days of tin extraction maybe over in the South West, but there is still some viable material left in the ground, and Wolf Minerals intends to get it.
The Drakelands Mine at Hemerdon near Plymouth is now operational, and the company believes it can produce 1,000 T/A of tin concentrate from the on-site processing plant.
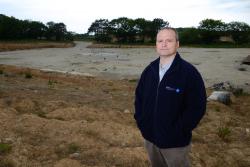
Chris Fraser, managing director and CEO of Sirius at the South shaft
The primary output from the mine is to be tungsten concentrate, with a target of producing 5,000 T/A, in fact it is one of only two mines outside of China with production capacity greater than 3, T/A.
The open site consists of a pit that will measure 850m long by 450m wide, extending to a depth of 260m. The non-hazardous waste is dealt with on-site at the mine waste facility (MWF).
Jeff Harrison, Wolf Minerals’ UK operations manager, told IME: “We’re very proud of what has been achieved here and the fact that the project build came in on time and on budget and we are now producing and shipping product to our customers overseas. We are currently still in a ramp-up phase as we move towards achieving full our production capacity which will see Drakelands Mine supplying 3-4% of the world’s tungsten as well as a smaller amount of tin.”
Going for gold
Galantas continues to explore for gold at its Omagh, County Tyrone, Northern Ireland site. Roland Phelps, president & CEO notes, “I am delighted with the drilling results so far. They continue to demonstrate why we believe Galantas holds an important high-grade gold property, which we expect to be brought into production in the near term. The discovery of a new high grade vein on our freehold land and the remarkable gold accumulation demonstrated by the recent core on Joshua, is the result of years of hard work by the Galantas geological team, building an ever more detailed picture of the Omagh gold deposits.”
The company recently drilled its largest high-grade accumulation, resulting in a find of gold grade of 9.9 G/T, 30.3 G/T silver and 0.6% lead, at an estimated vertical depth of 117.2m. Further drilling is planned, with three rigs currently on-site.
The company also has licence areas that are showing potential in the Republic of Ireland, some 33km south of Omagh.
Phelps continues, “We knew from our research and local knowledge that this package of licences was highly prospective for gold. To have identified gold and silver in outcrop so early in the program is exciting and I am delighted. To have interesting nickel and chromium results, in the same licence package, adds to our enthusiasm and demonstrates why we continue to explore the ROI licence area.”
A learning legacy
At one time the tin mining business in the South West of England was huge. It is thought that the material from Cornwall was traded around Europe for some 4,000 years, and from 1700 to 1914 there was intense mining activity. Also extracted were copper, arsenic, lead, zinc and silver.
As metal prices declined toward the end of the 19th century, mining in the South West became increasingly unprofitable. This caused large numbers of miners to take their specialist skills abroad, with Cornwall alone estimated to have lost up to half a million people from around 1815 to 1915.
So important is the area to UK history, in 2006 it was designated a UNESCO World Heritage Site.
With that wealth of history on its doorstep, it seems appropriate then that the local University of Exeter should house a specialist department, the Camborne School of Mines Research.
The facility manages its own test mine nearby, where students get trained how to drill, use explosives and conduct surveys.
Various research themes are actively being undertaken, including energy and resource efficiency, health and safety and environmental responsibility. There are around 25 people doing post-grad research, and over 30 technical papers were published last year.
Made in Scotland
With such a long history of mining it is no surprise to see thriving vehicle and equipment manufacturing industries in the UK.
Terex Trucks can trace its roots back to 1950 when US company Euclid started making off-highway trucks in Motherwell, central Scotland. In 1968 General Motors shed the Euclid brand and the new name was born, joining Terra (earth) and Rex (king). The Volvo Group acquired the company in 2014.
The company is in the process of renewing its range, the first new model to be launched this year is to be the 38 tonne TA400 articulated dump truck.
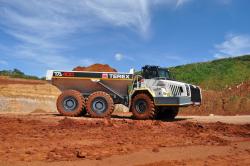
Terex Trucks’ latest (and biggest): the 38 tonne TA400
Terex claims: “To guarantee maximum uptime of the truck, investments have been made to ensure increased durability and protection of truck components, including upgraded hydraulic hoses, electrical interfaces, transmission mountings and brake pipes.”
More models in Terex Trucks’ new generation of articulated haulers will follow later in 2016 and 2017.
Source: Engineer Live